Ein neues Konzept-Rennrad von Decathlon erprobt die Möglichkeiten des 3D-Drucks aus Alu in der Fahrradproduktion. Die Studie erstellten die Designer mithilfe sogenannten „generativen Designs“ in Zusammenarbeit mit Software Hersteller Autodesk.
Der neue Rennrad-Prototyp soll selbstverständlich leicht und leistungsstark sein, aber auch nachhaltig. Er habe „das Potenzial für jeden Kunden, per 3D-Druck produziert zu werden“, heißt es in der Pressemitteilung des Software-Herstellers. „Da das Konzept vielversprechend erscheint, treibt das Design- und Entwicklungsteam die Tests weiter voran und wird zunächst Prototypen bauen“, sagt dazu Decathlon.
Im Rahmen des sogenannten „Vision Project“ erforschte der französische Hersteller und Einzelhändler von Sportartikeln die Möglichkeiten neuer, digitaler Fertigungstechnologien und Designideen. Konkret habe Decathlon mit Hilfe der generativen Designfunktionen von Autodesk Fusion 360 Komponenten für den Prototyp entworfen und hergestellt.
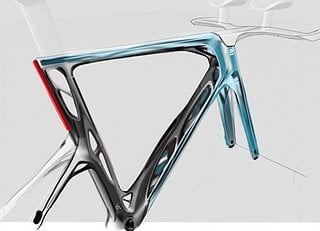
Das generative Design könne in Anwendungen wie dem neuen Rennrad-Prototypen komplexe Herausforderungen lösen, um die Qualität und Sicherheit des Rennrads zu gewährleisten. Dazu gehörte etwa die Entwicklung des Rahmens und der Federgabel, teilt Autodesk mit.
Obwohl der dargestellte Rennrad-Prototyp mit seinen organischen Formen nach Verbundwerkstoffen aussieht, handelt es sich laut Autodesk um einen Rahmen und Komponenten aus Alu 3D-Druck. Decathlon habe sich für den Einsatz von Aluminium entschieden, da die Kombination aus generativem Design und 3D-Druck die eingesetzten Rohstoffe reduziere und die Transportwege verkürze.
In einem Video, das zu dem Projekt veröffentlicht wurde, ist neben der auffällig gestalteten Gabel auch ein Helm ähnliches Objekt mit „Strebenstruktur“ zu sehen.
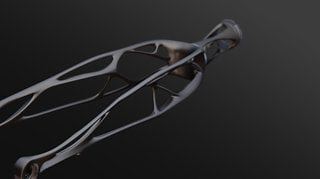
Decathlon wolle beobachten, wie generatives Design bereits in der Entwurfsphase angewendet werden kann um dazu beizutragen, den Kohlenstoff-Fußabdruck der Milliarden Ausrüstungsgegenstände, die jedes Jahr produziert werden, zu reduzieren, heißt es in einem Beitrag auf dem Portal Redshift zum Thema.
„Mit Hilfe der Tools von Autodesk vereinte Decathlon künstliche Intelligenz und menschliche Kreativität, um Nachhaltigkeits- und Leistungsziele zu verfolgen – und gleichzeitig die Wünsche und Anforderungen der Verbraucher zu adressieren“, sagt Scott Reese, Senior Vice President bei Autodesk.
Generatives Design ist eine Form von KI, bei der mit Hilfe der Cloud innerhalb kürzester Zeit eine Vielzahl an Designlösungen, die akkurat den Anforderungen und Bedingungen des Designers entsprechen, generiert und bewertet werden. „Mensch und Computer können auf diese Weise gemeinsam Objekte entwerfen, die über das menschliche Vorstellungsvermögen hinausgehen“, heißt es von Autodesk.
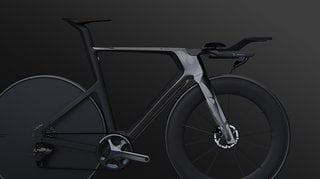
Was denkt ihr über Decathlons Ansatz zu größerer Fertigungsnähe?
15 Kommentare
» Alle Kommentare im ForumErinnert mich an den hier:
Vorbau
Ich habe Gefühl, daß die Mountainbiker im 3D Druck mehr ausprobieren.
ansich ist dass alles schon ein paar tage laenger moeglich, allerdings halt noch sehr teuer (wie normaler 3D Druck anfangs auch)
ich bin mal gespannt wann die ersten Laser 3D Drucker kompakt und bezahlbar sind
Ich wage mal die Behauptung aufzustellen, dass es noch lange dauern wird, bis 3D - Druck Massenkompatibel sein wird.
Bei Sonderanfertigungen oder wenn es wirklich um das letzte Quäntchen geht, hat das Verfahren echt seine Vorteile. Aber die Standzeit auf den Druckern ist noch zu groß im Vergleich zum Gießen und Nachbearbeiten bzw. gegen ein paar Rundrohre, die zusammengebrutzelt werden.
Bei der erreichbaren Festigkeit (im Vgl. zur ausgelegten Soll-Festigkeit) hätte ich per se erstmal wenig bedenken. Füllfaktoren nahe 100% sind beim Lasersintern schon jetzt kein Problem mehr.
Bei dem ganzen belastungsoptimierten Design ist sicher auch viel zu holen, aber die Krux liegt dabei in der Erzeugung der Lastprofile. Je vorhersehbarer die Belastungen, desto einfacher.
Optimiere ich ein Bauteil stringent nach auftretenden Lasten, dann habe ich auch nur dort Material, wo benötigt (wenn der Optimierer gut ist). Habe ich aber auch nur einen wesentlichen Lastfall vergessen (z.B. ein Querschlag in der Gabel, weil man mit dem Renner doch mal schräg auf nen Bordstein springen muss), ist eine Auslegung von klassischen fertigungsgerechten Geometrien typischerweise resistenter gegen diese Fälle. Klar kann man da mit diversen Sicherheitsfaktoren da entgegenwirken, die Frage ist dann nur, was dann noch rauszuholen ist.
Bei Metallen frage ich mich neben der Fertigungsdauer auch wie viel Potential des Materials sie überhaupt ausschöpfen wenn das ganze Objekt quasi nur aus Schweißnaht besteht. Es scheint da ja auch schon große Leistungsunterschiede zwischen geschmiedeten (gut) und gegossenen (bzw gefrästen, nicht so gut) Teilen zu geben. Würde mich nicht wundern wenn die gedruckten Varianten in dieser Hackordnung eine ganz neue Kellerliga eröffnen.
Wir laden dich ein, jeden Artikel bei uns im Forum zu kommentieren und diskutieren. Schau dir die bisherige Diskussion an oder kommentiere einfach im folgenden Formular: