Hopp Carbon Parts im Interview
MTB-News.de: Hallo ihr beiden, vielleicht fangen wir gleich mal mit einer kurzen Vorstellung an. Wer seid ihr?
Christoph Hopp: Mein Name ist Christoph Hopp, ich bin der Gründer und Geschäftsführer von Hopp Carbon Parts und stelle kleine Carbon-Fahrradteile her.
Axel Schnebelt: Ich bin Axel Schnebelt, bin 49 Jahre alt und Industriemechaniker und leidenschaftlicher Rennradfahrer, Mountainbiker und Leichtbauer. – Alles, was man noch leichter machen kann, wird angegangen.
Sehr gut. Und ihr stellt gemeinsam Carbonteile her. Wie kann man sich das Vorstellen?
Christoph Hopp: Ja genau, also das läuft bei uns so ab, dass ich die Carbonteile herstelle und Axel baut die Schaltwerke auseinander und die Carbonteile ein. Alles was Dreharbeiten, Fräsarbeiten angeht, übernimmt auch Axel. Gemeinsam tüfteln wir an neuen Ideen, Projekten und Verbesserungen.
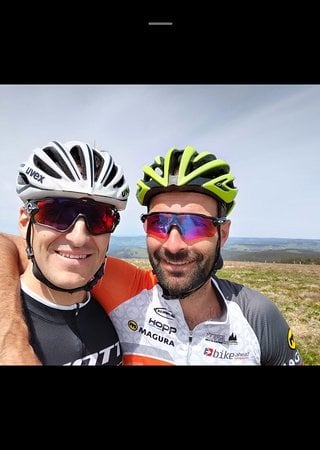
Wie kamt ihr dazu, gemeinsam Carbonteile zu bauen?
Christoph Hopp: Wir haben uns im IBC Forum kennengelernt. Axel hatte damals so ein leichtes 26″ Scott Scale aufgebaut, das auch mal Bike des Jahres geworden ist.
Axel Schnebelt: Genau, wir haben uns da über gemeinsame Interessen gefunden, und dann bei Projekten ausgeholfen.
Christoph Hopp: Das erste gemeinsame Projekt war der Umwerfer und das Schaltwerk für Axels Bike des Jahres. So hat sich das entwickelt und wir haben uns getroffen, gut verstanden und daraus ist eine gute Freundschaft entstanden.
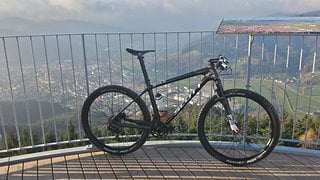
Axel hat ja schon erzählt, was er macht und gelernt hat. Christoph, was ist denn dein Background? Bist du da über das Hobby reingeschlittert oder hast du vorher schon was Handwerkliches gemacht?
Christoph Hopp: Ne, überhaupt nicht. Wahrscheinlich kann ich mich da bei meinen Eltern bedanken, dass ich grundsätzlich ganz geschickte Hände mit in die Wiege gelegt bekommen habe. Von meiner Ausbildung bin ich eher Kaufmännisch unterwegs gewesen und das hat sich tatsächlich echt alles so aus dem Hobby und aus learning by doing ergeben. Ich habe aber auch in meinem Freundeskreis einige Ingenieure, die ich dann anfangs auch um Rat gefragt habe. Das war nicht nur probieren und gucken. Mittlerweile hat man halt so viel Erfahrung und Gefühl für das Material und das Verfahren. Aber das ist eben kein Job, den man so lernen kann. Ich habe mir das alles angeeignet und teilweise selbst ausgedacht. Ein paar Geheimnisse stecken da ja noch dahinter. Am Ende ist es eine Mischung aus vielen Jobs, das kann man sich nur selbst beibringen.
Eure Ideen entstehen dann aus eigenem Antrieb nach Verbesserungen am Bike, oder wie läuft das bei euch ab?
Christoph Hopp: Genau, also eigentlich ist der Ursprung immer erstmal das eigene Bike. Man schaut an die eigenen Teile – wo kann man etwas noch leichter und besser machen. Dadurch, dass Axel Shimano am Mountainbike fährt und ich SRAM, haben wir da schonmal den Anspruch beide großen Marken abzudecken, damit unsere Bikes leichter werden. Im Rennradbereich fangen wir gerade erst an. Axel fährt dort SRAM. Ich bin nicht so oft auf dem Rennrad unterwegs und dadurch kam es, dass wir mit der SRAM-Schaltung angefangen haben. Axel hat mich da vor allem gepusht, denn wir haben im Mountainbike-Bereich schon jede Menge zu tun.
Axel Schnebelt: Ja, das typische Leichtbau-Auge schaut sich immer die Teile an und sieht dann mehr oder weniger Potenzial, um etwas zu erleichtern oder optisch upzugraden. Wenn man also die Möglichkeit hat …
Schaut ihr dann schon mit einem geübtem, scannendem Blick über die Teile und könnt direkt einschätzen, wo es sich lohnt ein Teil in Carbon zu fertigen, oder welches Teil schon sehr leicht konstruiert wurde?
Christoph Hopp: Ja genau, mittlerweile läuft das genau so ab.
Axel Schnebelt: Da gibt es auch einen kleinen Unterschied zwischen uns. Christoph rechnet gerne in Prozent. Wenn ich eine Schraube 45 min lang aus Aluminium fertige und die hat dann 0,8 g statt 2 g, dann sag ich, das mache ich nicht wieder. Christoph sieht dann eher die eingesparten 50 % und findet das super. In vielen Fällen probieren wir dann einfach bisschen rum und es entstehen coole Sachen.
Bei welchem Hersteller könnt ihr prozentual am meisten Gewicht rausholen, ist das eher bei SRAM- oder Shimano-Schaltwerken?
Christoph Hopp: Ich würde fast sagen, bei SRAM ist mehr zu holen, oder was sagst du Axel?
Axel Schnebelt: Ja, bei 12-fach-Schaltwerken, da ist Shimano meist schon etwas leichter.
Christoph Hopp: Es ist oft total nah beieinander. Letztendlich ist es auch ein wenig vom Schaltwerk abhängig und auch da muss man schauen, für wie viel man bereit ist. Bei den SRAM Transmission-Schaltwerken zum Beispiel haben wir so ziemlich alles ausgetauscht, außer der Feder und dem Motor. Man kann es dann schon ziemlich krass auf die Spitze treiben. Da ist prozentual schon einiges drin. Andererseits hat man bei alten SRAM-Schaltwerken fürs Rennrad dann schon ein Carbon-Parallelogram drin. Da ist nicht mehr so viel rauszuholen. Das variiert also schon.
Wie viel macht das dann bei einer Transmission aus?
Christoph Hopp: Also bei dem SL Schaltwerk, was an sich schon das leichteste ist und somit vielleicht das schlechteste Beispiel, da sind es dann so an die 90 g. Beim XX sind es ca. 95 g und beim X0 an die 100 g. Bei der GX könnte es noch mehr sein. Es ist aber schwierig zu sagen, weil die untereinander nochmal stark variieren. Da möchte ich mir demnächst nochmal die Mühe machen und einmal eine richtige Auflistung machen, mit den Gewichten von allen Schaltwerken und ihren einzelnen Teilen. Damit man sieht, wie viel hole ich bei welchem Schaltwerk an Gewicht raus. Um dann zu sehen, was ist dann wirklich die leichteste Basis für so ein Schaltwerk, da schon viel diskutiert wurde, ob es nicht das GX Transmission-Schaltwerk ist, was man am Ende am leichtesten bekommt.
Wenn ihr von den Herstellern SRAM oder Shimano jetzt die Sachen auseinandernehmt und durch eigene Teile ersetzt, haben sich dann schonmal die Ingenieure der Hersteller bei euch gemeldet, weil sie das cool finden oder so? Seid ihr da in Kontakt?
Christoph Hopp: Ja, also das ist schon ganz lang her. Es war gleich am Anfang mit dem Eagle-Schaltwerk von SRAM. Die hatten mich damals angeschrieben und nach Schweinfurt eingeladen. Da haben wir uns ausgetauscht, die fanden das cool, sie haben das auch von mir getestet und wollten nur sichergehen, dass das kein kompletter Schrott ist und sie ins schlechte Licht rückt, wenn da was kaputtgeht, aber ja, die fanden das cool. Jetzt sind wir nicht mehr so im direkten Austausch, aber man kennt sich, die wissen von den Produkten und ich kenn da auch den Manager aus dem Mountainbike-Bereich. Ab und an sieht man sich mal. Zum Beispiel auf dem Weltcup in Albstadt. Aber von Shimano hört man da nix. Zu SRAM ist dann schon eher die Verbindung entstanden, da sie hier in Deutschland ihre Produkte entwickeln.
Aber es kam jetzt noch kein Stellenangebot für dich, damit die Schaltwerke leichter werden?
Christoph Hopp: Nein, wenn man das wollte, würden die das natürlich auch können. SRAM hat da so viele gute Ingenieure, aber es ist ein viel zu hoher Aufwand, das würde sich einfach nicht rechnen.
Wo wir gerade bei Aufwand sind. Wie geht ihr ein neues Projekt an, wenn etwa ein neues Schaltwerk auf den Markt kommt?
Christoph Hopp: Also zuerst kaufen wir das Schaltwerk und dann haben wir früher die ganzen Werkzeuge selbst gemacht, Abdrücke gemacht und Formen gebaut. Seit dem Transmission-Projekt verfahren wir so, dass wir das Schaltwerk auseinandernehmen und dann wird das von einem anderen Unternehmen professionell eingescannt. Dann wird alles für die CNC-Fräse programmiert, sodass die Formen passen und alle Teile auch wieder herausnehmbar sind. Hier als Beispiel: Für das B-Knuckle der Transmission hat das Werkzeug 13 Einzelteile, damit man das Teil auch wieder aus der Form nehmen kann. Das ist ein riesengroßer Aufwand hinter den Formen und kostet natürlich entsprechend, aber Leute, die das verstehen, die verstehen dann auch, wie der Preis des Produkts zustande kommt.
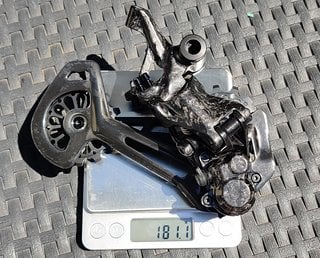
Wie viel kostet es dann seine Transmission leichter zu machen?
Christoph Hopp: Also wenn man einmal alles haben will, dann sind es schon ungefähr 1.000 €.
Bietet ihr auch andere Komponenten in leichter an? Habt ihr etwa was für die Kurbeln?
Christoph Hopp: Also Kurbeln explizit jetzt nicht, aber zum Beispiel bei der Quarq Powermeter Kurbel kann man die Abdeckung machen. Wir haben uns entschieden nichts anzubieten, was es schon auf dem Markt gibt, also Aheadkappen, Kurbeln, Sattelstützen. Da gibt es so viele auf dem Markt, die machen wir nicht.
Bei uns im Team haben manche schon angefangen Kettenführungen zu basteln. Da wurden sich Carbonmatten bestellt und dann gings los.
Christoph Hopp: Ja, genau damit habe ich auch angefangen. Kettenführungen und Schaltwerkskäfige, damit hat bei mir vor 25 Jahren alles angefangen.
Du laminierst dann selbst bei dir zu Hause und testest, ob die neuen Formen passen?
Christoph Hopp: Ja, genau das ist auch immer gut, wenn gleich alles passt, weil so ein Werkzeug kostet schon einiges. Ein günstiges kostet so 2.000 € und das teuerste, was mir mal angeboten wurde, ist das 13-teilige Werkzeug für den Transmission B-Knuckle, das kostet 16.000 €. Deshalb gibt es das auch noch nicht. Da müsste man das Teil für an die 1.000 € verkaufen und das rechnet sich einfach nicht. Die Stückzahl erreichen wir gar nicht. Also von dem alten AXS Schaltwerk habe ich etwa 100 Stück gebaut.
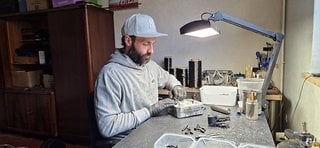
Wie lange dauert es so ein Teil zu laminieren und der ganze Prozess?
Christoph Hopp: Das variiert. Bei manchen Teilen braucht man für ein Einzelteil ungefähr eine Stunde, um es zu laminieren. Je komplexer ein Teil ist, desto länger dauert es. Bei manchen Teilen braucht man auch nur maximal 10 Minuten. Das B-Knuckle ist das komplexeste Teil am Schaltwerk und dauert am längsten. Dann gibt es noch die beiden H-Gelenke, wie wir sie nennen, die das Parallelogramm ergeben. Dabei ist es besonders wichtig, alles genau und präzise zu bauen. Die Positionen der Achsen müssen stimmen. Beim alten B-Knuckle hatte man noch die drei Einstellschrauben dran, die müssen natürlich ihren Platz haben. Und die Kunst ist es dann, das Teil so zu bauen, dass alles passt. Gerade das Ein- und Ausbauen aus dem Werkzeug ist eine große Schwierigkeit, weshalb es vermutlich auch nicht viele machen außer uns.
Habt ihr dann etwa in den Parallelogrammen noch Gleitlager drin?
Christoph Hopp: Nein, also wir versuchen die Teile möglichst original nachzubauen, damit sie dann auch weiterhin untereinander mischbar sind. Wenn also im Originalteil eine Buchse ist, dann ist in unserem Teil auch eine Buchse.
Und die Schaltwerke baut ihr dann auf Bestellung? Oder hast du die schon fertig bei dir liegen?
Christoph Hopp: Genau, ich baue die immer auf Bestellung. In den vergangenen Jahren habe ich es nie geschafft, ein Lager zu haben. Wenn, dann hab ich mal noch ein paar Air Caps mitgemacht, wenn noch ein bisschen Material übrig ist. Dadurch habe ich ein Bisschen was auf Lager, aber das sind ganz, ganz geringe Stückzahlen. Aber eigentlich mache ich das auf Bestellung.
Für viele ist ja die Einstellung von der Schaltung schon ein Ding der Unmöglichkeiten. Ihr baut die Schaltwerke auseinander und wieder zusammen. Gibt’s da irgendeinen Endgegner, der einfach abartig kompliziert ist oder sind die alle schwierig? Wie kann man sich das Vorstellen, denn es gibt schließlich keine Anleitung dafür.
Axel Schnebelt: Ja, davon kann ich Geschichten erzählen. Also beim Red-Schaltwerk wird der Akku von so einer kleinen Klappe gehalten, die man öffnen muss, dass der Akku abnehmbar ist und da geht eine 1,5 mm Achse durch, die den Drehpunkt generiert und die ist einmalig da reingepresst. Also die bekommt man nicht raus und bevor die Klappe oder die Verriegelungsklappe nicht weg, ist bekommt man die Kunststoffumhausung vom Akku nicht demontiert. Das ist natürlich ein Kunstwerk bzw. ein Zaubertrick die 1,5 mm Achse zu entfernen, dass man die Akkuhalteklappe entfernen kann.
So Sachen, da denkt man dann schon ewig drüber nach, wie bewerkstellige ich das, bzw. ich mache das Gelenk in dem Fall des B-Knuckle nicht kaputt, es muss ja alles wieder positionierbar sein für Christoph, dass er das Teil dann in Carbon herstellen kann. Also da muss man dann schon fast chirurgisch vorgehen und wir zerbrechen uns die Köpfe, wie das klappt.
Christoph Hopp: Der richtige Endboss ist im Moment das Dura Ace-Schaltwerk. Da gibt es viele Anfragen und viel Interesse, aber da hat man schon Angst, man macht es kaputt, wenn man es zerlegt.
Axel Schnebelt: Ja, das Dura Ace habe ich mir angeschaut. Irgendwie bekommt man es schon auf, aber es ist viel aufwendiger, als ein SRAM, wobei ich auch das SRAM schon aufwendig finde.
Wie läuft so eine Bestellung dann bei euch ab? Bestelle ich bei euch ein komplett umgebautes Schaltwerk, oder kaufe ich das selbst und schick es zu euch und ihr baut es mir um? Wie funktioniert das?
Christoph Hopp: Das kommt ein bisschen drauf an. Also das Red Schaltwerk z.B. das machen wir nur so, dass die Leute entweder ihr Schaltwerk schicken oder ein komplett umgebautes kaufen. Weil es halt einfach zu umständlich ist den Leuten das zu erklären, wie die das auseinander bekommen. Da musst du echt schon ein paar Schaltwerke zerlegt haben, damit du weißt, was du zu tun hast. Das ist bei den wenigsten der Fall. Das genaue Gegenteil ist das Transmission-Schaltwerk. Da hat SRAM das schon sehr anwenderfreundlich gestaltet und man kann es mit einem Inbus komplett auseinander schrauben. Da kann der Kunde jedes Teil einzeln kaufen: Der eine kauft nur eine Abdeckung, der andere den Käfig, einer wiederum dann das ganze DIY Kit. Da gibt es alle Möglichkeiten. Aber man kann auch weiterhin sein Transmission-Schaltwerk einschicken und wir bauen die auseinander und wieder zusammen. Da bekommt man seine alten Teile natürlich auch wieder mit zurück, falls man es als Ersatzteil braucht.
Gibt es da Unterschiede in der Schaltperformance? Es wird ja gekauft, um etwas Exklusives zu haben, das leichter ist. Wie schaltet sich das, wie fühlt sich das an?
Christoph Hopp: Also mittlerweile merkst du keinen Unterschied. Das fühlt sich ganz genauso an. Die Werkzeuge, die wir jetzt haben, sind so genau. Ich fahre jetzt selber auch an meinem Mountainbike die ganze Zeit die Transmission-Schaltung, und auch die Kunden. Also da hat jetzt noch keiner irgendwie gesagt, dass irgendwas nicht gut funktioniert, nicht gut schaltet. Es gab andere Zeiten, das ist jetzt ein paar Jahre her. Wir haben uns das ja alles selber angeeignet, die Fähigkeiten, wie man so Werkzeug baut und wie man die Teile baut und da macht auch Fehler, aber mittlerweile sind die so genau, dass die Performance genauso ist wie beim Original.
Axel Schnebelt: Genau das Red, was ich jetzt fahre, das ist das Erste gewesen und das B-Knuckle ist wirklich super klasse. Es ist total in der Geometrie perfekt und es schaltet wunderbar.
Christoph Hopp: Wir fahren die Sachen erstmal und probieren das zunächst selbst. Man kann da mittlerweile nicht mehr irgendwas verkaufen, wo man nicht weiß, ob es funktioniert, weil das nehmen die Leute sehr schnell übel und das spricht sich rum. Dann stehst du da.
Was denkt ihr, warum investieren die Leute noch mal so viel Geld, um ihre funktionierende Schaltung abzuändern?
Christoph Hopp: Eigentlich zwei Gründe: also entweder ästhetische Gründe oder wirklich Gewicht. Es gibt wirklich viele Leute, die das so vorträumen, Dangerholm zum Beispiel. Der dann eben zeigt wie leicht man so ein Fahrrad doch haben kann und was noch alles so rauszuholen ist und das war letztlich auch an unser Ursprung damals. Dass wir selber auch Räder hatten und dann hast du dir alles gekauft, was es so gab und warst nicht zufrieden, wolltest es doch nochmal leichter oder individueller haben und ich denke mal, genau das sind auch die Anreize von den Leuten, die das kaufen.
Axel Schnebelt: Genau, das Individualisieren, die Begeisterung, technisch begeisterte, da gibt es so viele Aspekte, Empathie.
Christoph Hopp: Ja stimmt. Viele meiner Kunden kommen aus technischen Berufen, die wirklich Ingenieure sind und das Verständnis haben und dann auch Freude an diesen technischen Sachen haben.
Axel Schnebelt: Aber auch auf der anderen Seite habe ich auch Leute bei mir, ich biete auch noch andere Sachen an, ich mache Carbon-Steckachsen und und und – kleine Behilflichkeiten, da gibt’s auch Leute, die haben wirklich im Prinzip zwei linke Hände, die so Sachen kaufen und dann Unterstützung brauchen, die man berät und anleitet, wie das zu handhaben ist, oder zu montieren, also es ist einfach nur Begeisterung für Technik.
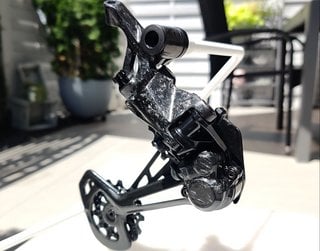
Warum verwenden die Hersteller nicht noch mehr Carbon in ihren Schaltwerken?
Christoph Hopp: Kostengründe hauptsächlich. So ein Carbonteil ist wirklich ein Vielfaches aufwendiger als die verwendeten Teile. Die werden gepresst oder gefräst, aber das ist ein Prozess, da kommt nicht wirklich Handarbeit mit ins Spiel. Weil wenn du so ein Carbonteil machst, und gerade, wenn du es auch stabil machen willst, weil das Verfahren, wo du einen Brei mit Kurzfasern irgendwo reinpresst, das Verfahren hat ja irgendwo seine Grenzen. In unseren Teilen sind endlos Fasern drin. Sozusagen nicht nur kurze Stücke, sondern die sind innen drin belastungsgerecht aufgebaut, dass man dann da, wo die Kräfte fließen auch durchgängige Fasern hat, die das auch abkönnen.
Ihr macht euch dann schon Gedanken wie beim Rahmenbau, dass ihr die entsprechend legt und euch ein Layup ausdenkt?
Christoph Hopp: Ja, nicht so komplex wie in einem Rahmen, wo die Fasern in bestimmte und verschiedene Richtungen gehen, sondern bei unseren Teilen, einem H-Gelenk zum Beispiel, da sieht man dann schon in etwa, wo die Kräfte laufen und wir schauen, dass wir die Fasern entsprechend von dem einen Gelenk zum anderen legen und die verbinden.
Schaltrollen aus Carbon, warum macht ihr das nicht? Oder gibt das von anderen Anbietern?
Christoph Hopp: Ja, das habe ich schon gesehen, aber ich finde es Quatsch, weil so ein Serien-Röllchen ist genauso leicht, aber am Ende einfacher herzustellen, leiser und langlebiger. Das ist einfach nicht das richtige Material dafür.
Axel Schnebelt: Ich habe das vor Jahren zur Genüge ausprobiert und kaputt gemacht, die selbst gefertigt. Also der Verschleiß ist exorbitant höher durch Schmutz und alles nutzt sich das Carbon am Reibpartner ab. Deswegen auch Carbon-Kettenblätter: Das ist das falsche Material am falschen Einsatzort. Der Verschleiß ist einfach zu hoch. Wenn man da Extralite mit ihren Schaltröllchen sieht, die haben so gut wie fast gar keinen Verschleiß. Also weniger Verschleiß als ein Shimano- oder ein SRAM-Röllchen und es wiegt im Prinzip das Gleiche. Deshalb hat Gemini unter ihrem Rigel Carbon-Kettenblatt Titanzähne drunter. Das sieht cool aus, aber das Carbon verschleißt sehr schnell.
Wenn sich Leute mit euch austauschen wollen: Seid ihr bei uns im Leichtbau-Forum unterwegs?
Christoph Hopp: Ich eher nicht, aber Axel ist da bekannt. Ich habe immer viel zu tun und da fehlt einfach die Zeit.
Okay, dann jetzt die letzte Frage: Habt ihr ein Lieblingsteil, das ihr gemacht habt?
Axel Schnebelt: Ich finde, es sind alle Teile Lieblingsteile, weil jedes hat eine Geschichte, einen Ursprung und ich freue mich dann immer wieder das Aluminiumteil in der Hand zu haben oder was es auch war, aus Kunststoff, und dann das Neue aus Carbon im Vergleich zu haben, was Christoph da hinzaubert. Deswegen würde ich sagen: alle Teile. Aber das geilste Teil ist eigentlich der Trickstuff Carbon-Hebel. Vor allem mit dem Hintergrund, wie man zu dem fertigen Produkt gekommen ist. Da haben wir unzählige Stunden philosophiert und ausgedacht, wie kann das Werkzeug aussehen soll und so weiter. Dabei ging es aber nur um den Prototyp. Die finale Serienversion, die Christoph gemacht hat, war dann etwas anders.
Christoph Hopp: Ja, der ist mir auch so durch den Kopf gegangen, die habe ich ja eine Zeit lang gemacht. Und das Ergebnis war schon toll, wobei der Weg dahin das eben nicht war. Deswegen vielleicht doch nicht das Lieblingsteil. Mein aktuelles Lieblingsprojekt ist die Transmission-Schaltung und die Red wird bestimmt auch noch toll, wobei das XTR Schaltwerk ist auch schon schön …
Axel Schnebelt: Ja, puh, das stimmt. Vor allem mit dem B-Knuckle, da habe ich anfangs echt gezweifelt, weil es so viele Hinterschritte hat. Christoph war da von immer begeistert und so ist es auch gekommen, als es aus der Form kam, das war tiptop, das ist mittlerweile echt Highquality.
Danke euch beiden für das spannende Interview und die Einblicke.
Mehr zu Hopp Carbon Parts auf der Website
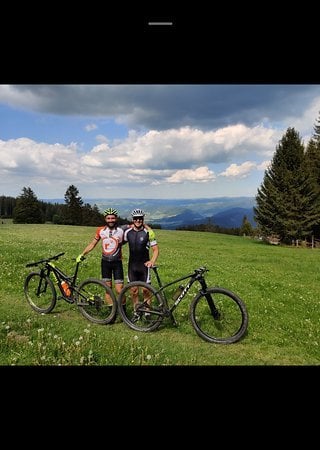
Was sagt ihr zum Thema Leichtbau? Habt ihr euer Bike in der Hinsicht getuned?
11 Kommentare
» Alle Kommentare im Forumhttps://www.mtb-news.de/forum/t/scott-scale-rc-worldcup-custom.826040/post-17789126
Oder hier Schaltwerkstuning:
https://www.mtb-news.de/forum/t/scott-scale-rc-worldcup-custom.826040/post-16765689
Am lehrreichsten ist es den ganzen Thread mal kurz zu überfliegen, da sind einige Perlen drin versteckt.
Mit CAD arbeiten die übrigens gar nicht.
sympathische Typen, toller Ansatz - hoffe, die können sich dauerhaft behaupten!
tolle teile!
wäre schön, so etwas mit aller sorgfalt handgefertigtes am rad zu haben.
muss ich halt woanders sparen;-)
diesmal wirkliche Handwerkskunst. Die Fraezen Parts werden inzwischen auch in China hergestellt. Nix mehr Allgäu
Wir laden dich ein, jeden Artikel bei uns im Forum zu kommentieren und diskutieren. Schau dir die bisherige Diskussion an oder kommentiere einfach im folgenden Formular: